Flour is a staple food that has been consumed by humans for thousands of years. From ancient civilizations to modern societies, flour has played a crucial role in providing nourishment, sustenance, and culture. However, the production of flour requires advanced technology and equipment, one of which is the flour mill machine.
Flour mill machines use a series of rollers to crush and grind grains into flour, and the quality and efficiency of these rollers depend on the materials and processes used to make them. In this article, we will take a closer look at the manufacturing process of alloy rolls for flour mill machines, and explore the science and art of creating these essential components.
The first step in making alloy rolls is to select the right materials. Alloy rolls are typically made of high-quality steel or iron, which is mixed with other elements, such as chromium, molybdenum, and vanadium, to enhance their strength, hardness, and wear resistance.
The exact composition of the alloy depends on the specific requirements of the flour mill machine, such as the type of grain, the desired fineness of the flour, and the operating conditions. The alloy is melted in a furnace and poured into a mold, which has the shape and dimensions of the roll.
Once the alloy has solidified, the mold is removed, and the roll is ready for further processing. The roll is placed in a lathe, which is a machine that rotates the roll and removes any excess material from its surface. The lathe also creates grooves or flutes on the roll, which help to grip and move the grains as they pass through the mill.
The depth, width, and spacing of the grooves depend on the type of grain and the desired texture of the flour. The lathe uses special cutting tools, such as carbide inserts, to achieve precise and smooth cuts.
After the lathe, the roll undergoes several heat treatments, which involve heating and cooling the roll to specific temperatures and durations. Heat treatments help to refine the microstructure of the alloy, improve its hardness and toughness, and relieve any residual stresses from the manufacturing process. Heat treatments also allow the roll to maintain its shape and performance under high loads and temperatures, which are typical of flour mill machines. The exact parameters of the heat treatments depend on the alloy, the roll size, and the desired properties.
The final step in making alloy rolls is to inspect and test them for quality and performance. Rolls are inspected for defects, such as cracks, pits, or uneven surfaces, which can affect their function and safety. Rolls are also tested for hardness, wear resistance, and surface finish, using specialized equipment, such as durometers, abrasion testers, and surface profilers. The results of the tests are compared to the specifications and standards of the flour mill machine, and any deviations or issues are addressed before the rolls are shipped to the customers.
In conclusion, the manufacturing process of alloy rolls for flour mill machines is a complex and fascinating endeavor that combines metallurgy, machining, and quality control. Alloy rolls are essential components that enable flour mill machines to produce high-quality and consistent flour, which is critical for the food industry and consumers. By understanding and appreciating the science and art of making alloy rolls, we can gain a deeper insight into the modern world of food production and technology.
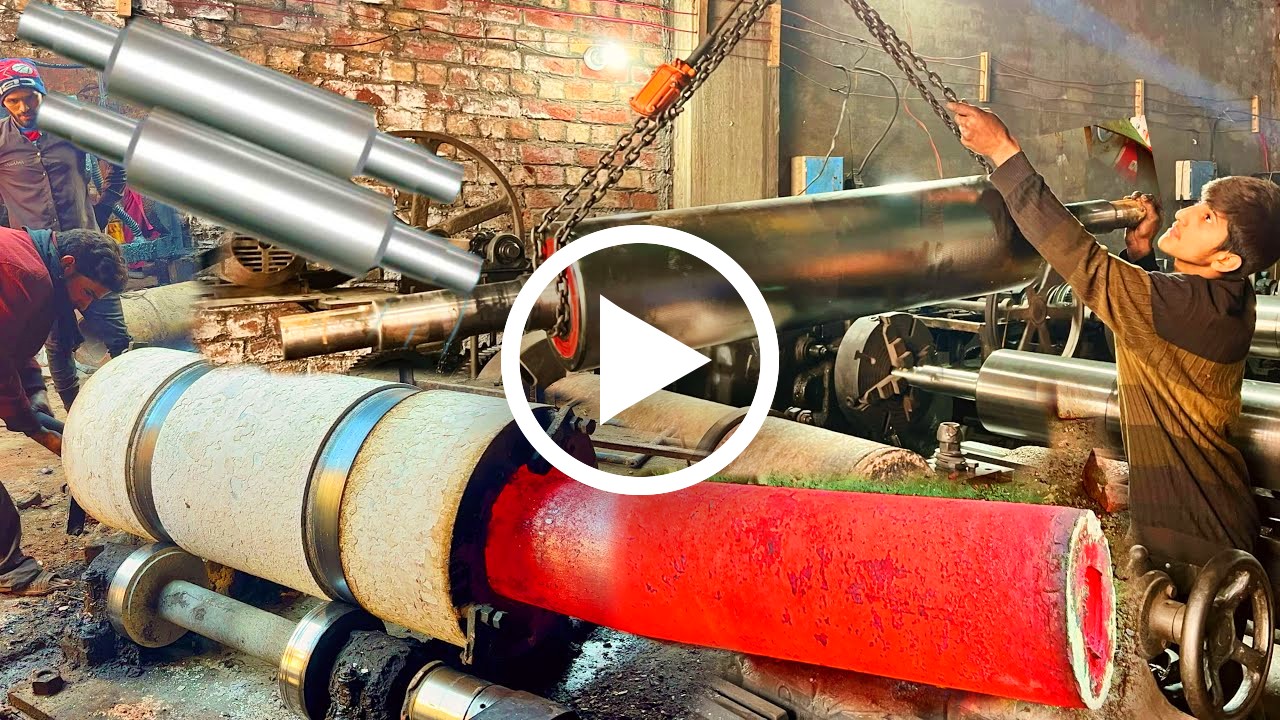